Modeling propeller in heliciel software
Tutorial design a boat propeller (4) Selection and optimization profiles propeller blade
Understand and master the boat screew propeller design lesson(4/5): Selection and optimization profiles propeller blade:
We can be satisfied with our propeller built in the Tutorial design a boat propeller (3)because it close enough to our specifications to be acceptable, and performance of 0.79 is very honorable!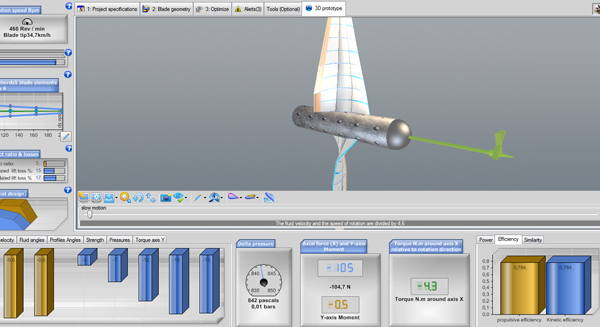
But to go further in control of the design, we will see how to assign the best possible profile in our propeller blade, and thus enter into the analysis of the profiles.A propeller blade is a rotating wing.This is the lift force of our rotary wing that generates thrust , and the drag force of our rotary wing generates resistive torque that will provide the engine with the propeller shaft. A good profile generates a lot of lift and low drag. (And must not cavitate .. but it is a further Question which we will discuss later)
- The quality of a profile so his lift / drag ratio,
- CL(lift coefficient of 2d profile) / Cd(drag coefficient 2d profile).
lift/drag ratio anf lift according to Reynolds numbers in the interactive data base included in Heliciel software:
All blade elements do not work with as much efficiency, a component near the axis provide little lift because its speed is low, a blade tip element generate many lift,but losses wingtip will decrease the effectiveness of this lift. (Unless the blade is equipped with winglets or shroud reducing losses) For these reasons, in practice, the area of the blade that provides more lift is usually located around 0.75 times the radius of the blade. We have every interest to care for this area of the blade and choose the appropriate profile for the velocity at the 0.75 radius element!
In this tutorial we have chosen the law of constant profile. This implies that the shape of the profile will be the same all along the blade. We have to choose what will be the speed (Reynolds number) that will determine the performance profile. We will choose the speed of the blade element the most effective:
We will find the profile that gives us the best lift/drag ratio, at Reynolds number of the element at 0.75 times the radius, and apply it to our propeller blade. To show Reynolds number of the element generating more thrust, use thrusts graphic to see which element generates more thrust (note that is about 0.75 times the radius)
- The Reynolds number at the base profile is given by: Reynolds = 245 618
- We take this opportunity to note the lift/drag ratio of the current profile (top left of the image of the profile)Fin.max: 45.43
We are looking for a profile whose finesse is greater than 45.43 for a Reynolds number around 200,000.Select and apply the best lift/drag ratio profiles to the propeller blade:
- Show database profiles : (2 quick ways to display the database)
- 1: By clicking on the blade in the 3d model, the profile of the selected item is displayed:
- 2:In the tool bar at the bottom of the Windows desktop,the database is always ready to be consulted:
clicking the left mouse button on the image profiles to show the interactive database
The naca64a410 profile lift/drag ratio is 78.5, We therefore choose it as the default profile for all elements of our blade : For this, it suffices to click "default profile (profile law)"
and our propeller is rebuilt with the selected profile: